Porosity in Welding: Identifying Common Issues and Implementing Finest Practices for Prevention
Porosity in welding is a pervasive issue that often goes undetected till it triggers considerable problems with the integrity of welds. This usual flaw can jeopardize the strength and resilience of bonded structures, positioning safety threats and bring about expensive rework. By understanding the root triggers of porosity and applying reliable prevention strategies, welders can significantly boost the high quality and integrity of their welds. In this discussion, we will check out the vital elements contributing to porosity formation, analyze its destructive results on weld performance, and discuss the most effective techniques that can be adopted to minimize porosity occurrence in welding procedures.
Typical Sources Of Porosity

Utilizing dirty or damp filler products can introduce impurities right into the weld, adding to porosity problems. To mitigate these usual reasons of porosity, comprehensive cleansing of base steels, proper securing gas choice, and adherence to optimal welding criteria are vital practices in accomplishing high-quality, porosity-free welds.
Influence of Porosity on Weld Quality

The visibility of porosity in welding can substantially compromise the structural stability and mechanical properties of welded joints. Porosity produces gaps within the weld steel, compromising its total toughness and load-bearing capacity.
One of the main repercussions of porosity is a decline in the weld's ductility and durability. Welds with high porosity degrees often tend to exhibit lower effect stamina and minimized capacity to flaw plastically prior to fracturing. This can be particularly concerning in applications where the welded components are subjected to vibrant or cyclic loading conditions. Porosity can impede the weld's ability to properly transmit pressures, leading to early weld failing and possible safety hazards in critical structures. What is Porosity.
Best Practices for Porosity Prevention
To enhance the architectural integrity and quality of welded joints, what particular measures can be carried out to lessen the incident of porosity during the welding procedure? Porosity avoidance in welding is important to make sure the honesty and stamina of the last weld. One reliable technique is appropriate cleansing of the base steel, removing any kind of contaminants such as corrosion, oil, paint, or wetness that could lead to gas entrapment. Ensuring that the welding devices is in excellent condition, with tidy consumables and suitable gas circulation rates, can additionally substantially reduce porosity. In addition, preserving a secure arc and managing the welding have a peek here criteria, such as voltage, present, and take a trip speed, aids create a constant weld pool that lessens the threat of gas entrapment. Utilizing the proper welding technique for the certain product being welded, such as readjusting the welding angle and gun setting, can view it now better avoid porosity. Regular examination of welds and instant remediation of any kind of problems identified throughout the welding process are essential methods to stop porosity and produce top notch welds.
Significance of Proper Welding Techniques
Carrying out proper welding strategies is vital in guaranteeing the architectural stability and top quality of welded joints, building upon the structure of effective porosity avoidance measures. Too much heat can lead to raised porosity due to the entrapment of gases in the weld pool. In addition, utilizing the ideal welding specifications, such as voltage, existing, and travel rate, is vital for attaining sound welds with minimal porosity.
In addition, the selection of welding procedure, whether it be MIG, TIG, or stick welding, ought to line up with the particular needs of the task to guarantee optimal results. Proper cleansing and preparation of the base steel, in addition to selecting the appropriate filler product, are also important parts of skillful welding techniques. By adhering to these finest methods, welders can decrease the risk of porosity formation and generate high-quality, structurally sound welds.
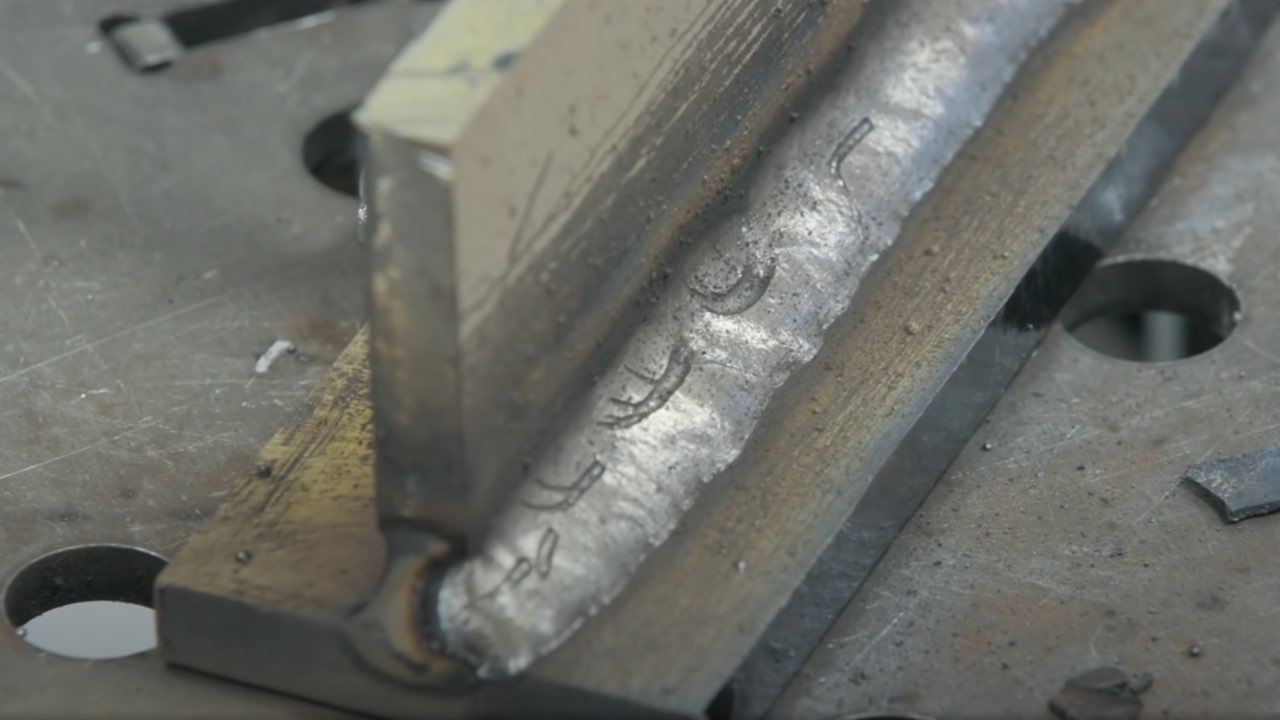
Evaluating and Quality Assurance Measures
Checking treatments are essential to find and protect against porosity in welding, making certain the stamina and toughness of the final product. Non-destructive testing techniques such as ultrasonic testing, radiographic testing, and visual evaluation are frequently used to recognize possible defects like porosity.
Carrying out pre-weld and post-weld examinations is additionally critical in maintaining quality assurance standards. Pre-weld inspections involve validating the materials, equipment setups, and cleanliness of the job location to avoid contamination. Post-weld examinations, on the other hand, assess the last weld for any issues, including porosity, and validate that it satisfies defined criteria. Applying an extensive quality assurance plan that consists of complete testing procedures and inspections is extremely important to minimizing porosity concerns and guaranteeing the general quality of bonded joints.
Final Thought
In verdict, porosity in welding can be a common problem that affects the top quality of welds. By recognizing the typical root causes of porosity and applying finest practices for avoidance, such as proper welding browse this site strategies and testing measures, welders can guarantee top quality and trustworthy welds. It is important to focus on avoidance methods to decrease the occurrence of porosity and maintain the integrity of welded structures.